In Solution Controller
The heart of our system is the controller. This controls the dosing pump that delivers the concentrated supplements into the drinking water. It also monitors the tank levels and can connect to satellite to stream data to your computer or phone.
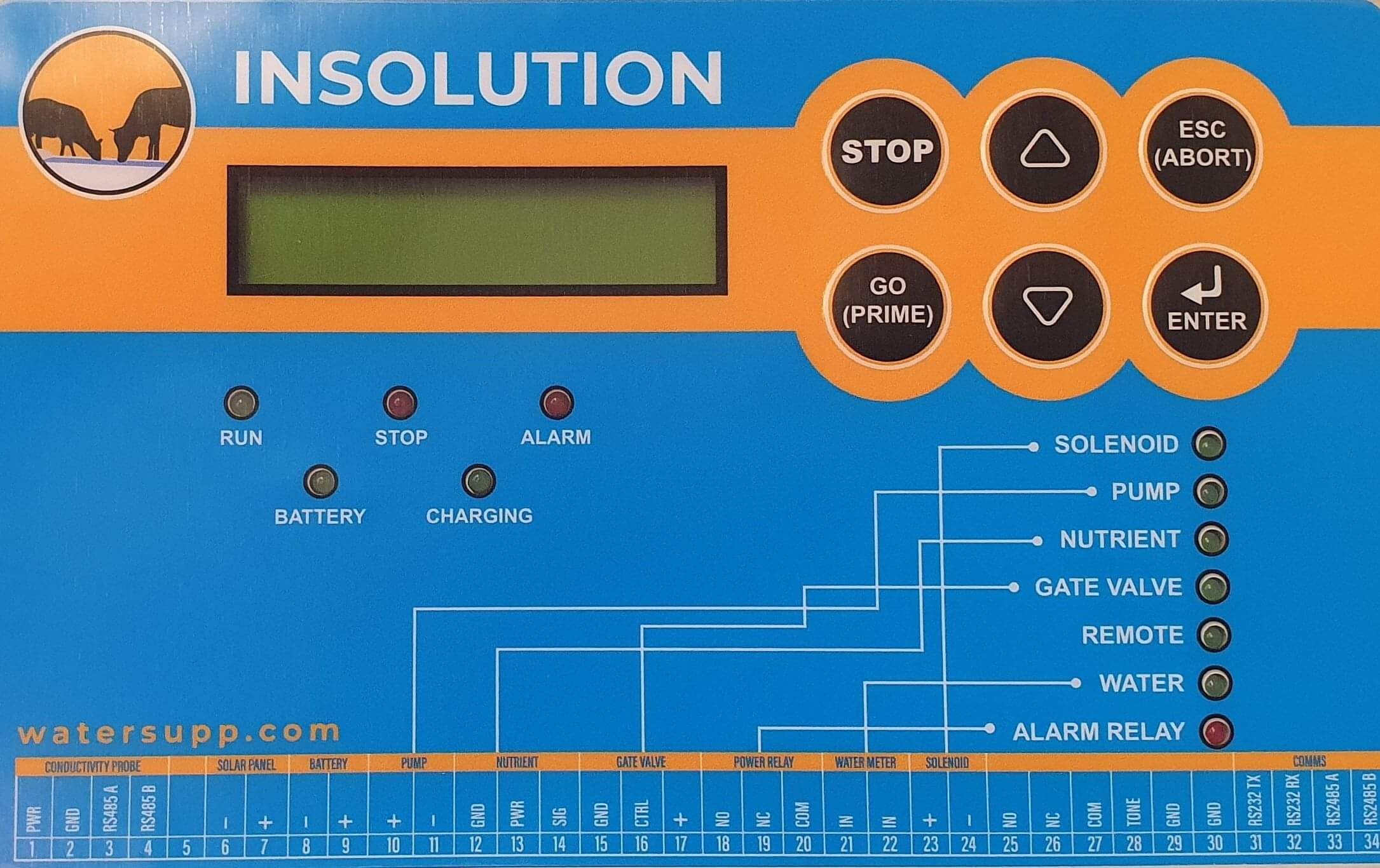
Existing Dosing Equipment
Many producers have existing dosing equipment. The major brands are Nutridose and the Udose, however some Norprim injectors are still operational.
Our team is able to service these units when required on a back to base basis.
Our basic controller is now available for Norprim upgrades. Depending on the condition you may be able to replace the Norprim controller with our In Solution controller, however we use a water meter with a 10 litre pulse, so you may be able to change the register on your existing meter, or you will need a new one. The Norprim, pictured here, was just upgraded.
Contact us if you need repairs to your existing controllers.
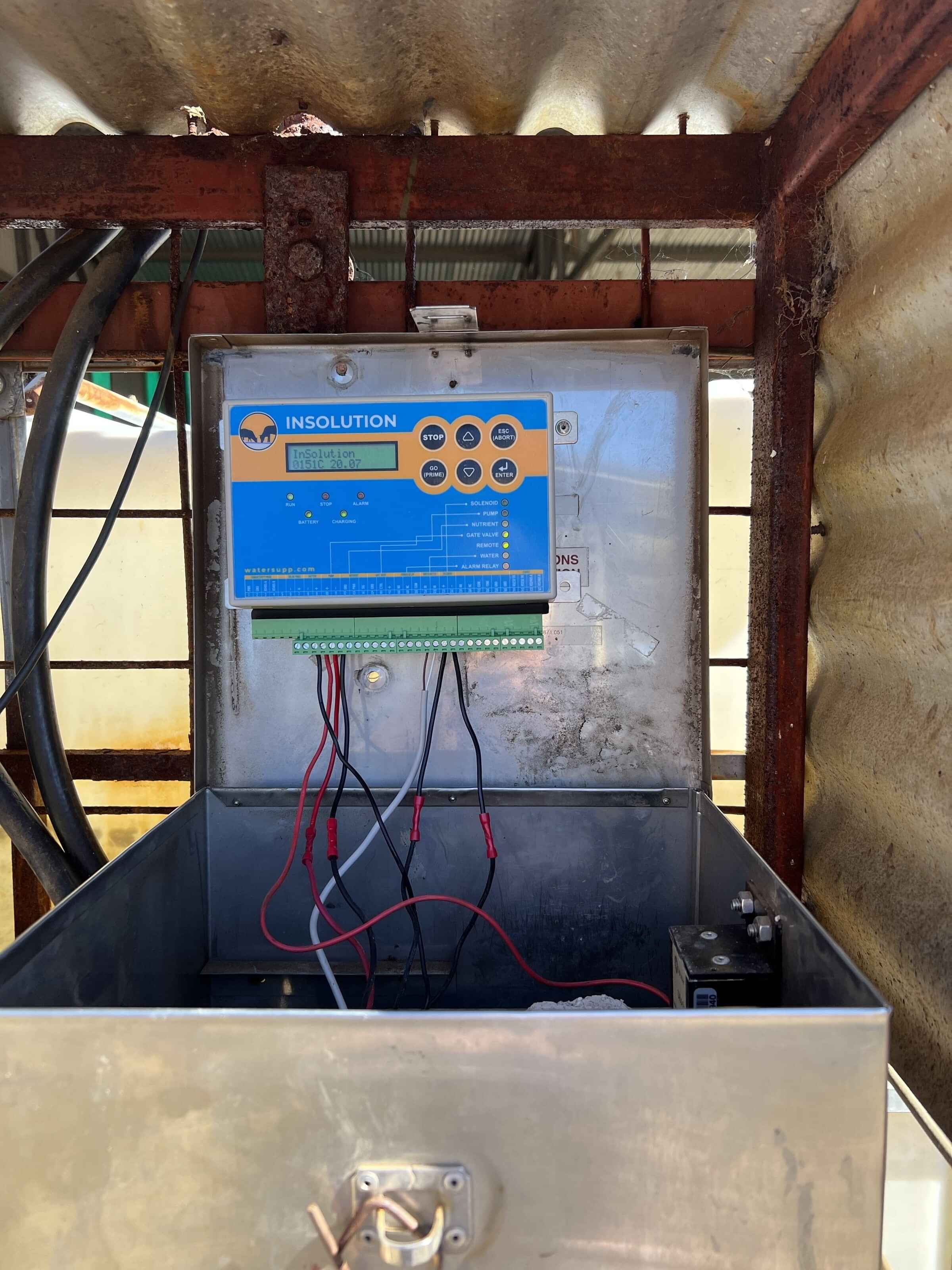
New Dosing Equipment
In Solution Proportional Dosing Unit
In designing this new hardware for water supplement systems, we have gone back to basics and using the experience developed in the field, we have focused on building in increased reliability by addressing those areas that cause frequent alarm states and reduce overall operability by having units offline for extended periods. We have also reviewed all aspects of the unit with an eye to cost savings where possible and increasing the quality of components where applicable.
Over 30 years of experience has demonstrated that the most reliable method of delivery is the timed injection. Once this is calibrated for individual system the unit it remains consistent and is monitored by checking the use rate of the concentrate tank against the water used as measured by the water meter. Minimal maintenance is required with this method, however the normal safety features that will shut the system down if the pump is on too long or skipping an injection if double signals are received from the main water meter are detected, will remain.
The unit will be fitted with a 316 stainless steel solenoid cutoff valve to ensure the concentrate tank is isolated when the pump is not active.
Injectors using measured volume injection, whilst good in theory, have demonstrated to be consistently unreliable in the real world. They are prone to error due to calcite build up, susceptible to undissolved solids passing through, and require a high level of maintenance to ensure they remain accurate and fit for purpose. While some of these problems have been overcome by using ultrasonic flow meters, these are still subject to unreliability due to temperature constraints and the concentration of the injection solution and continue to cause false alarm states in the field that shut the unit down. As well as this, the cost of these ultrasonic flow meters is considerable.
By using timed injection, we have a basic, reliable system that is consistent and will still use a flow meter to measure flow, however this is not used to control the flow. The 1 second to 10 litres gives a reliable 1:100 ratio.
While measuring the electrical conductivity of the water has proven to be additionally useful as a safety mechanism, experience has shown that conductivity probes being installed in livestock grazing water systems are subject to contamination with calcite, microbial build up, bubbles in the water, temperature variation and possible electrical interference, again triggering false alarms, leading to higher maintenance requirements, and reducing the efficacy of the system.
In response to the challenge of maintaining safety, In Solution has developed a pressure sensor to monitor the nutrient levels of the concentrate tank. Once a concentrate tank system has been properly set up, the level of concentrate and the usage rate of the concentrate can be accurately determined with the data being able to accurately determine if the correct dilution rates are being delivered and provide a safety mechanism in the event of detecting that too much nutrient is being delivered. This feature will replace the conductivity monitor as it provides equivalent data in regard to monitoring injection rates and is more reliable in practice.
All the data from the In Solution dosing unit is at your fingertips through satellite communication.
In terms of increasing quality, we have mounted the unit in a 316 Stainless Steel enclosure that is designed to hang on the side of an IBC concentrate tank.
Solar power has been increased by fitting 100 watt panels to ensure increased charging rates and battery power increased to 115 Amp Hours to cover high use situations.
Stainless steel water meters are also available.